The Double Pig System Working Principle: A Breakthrough in Efficient Pipeline Cleaning and Product Recovery
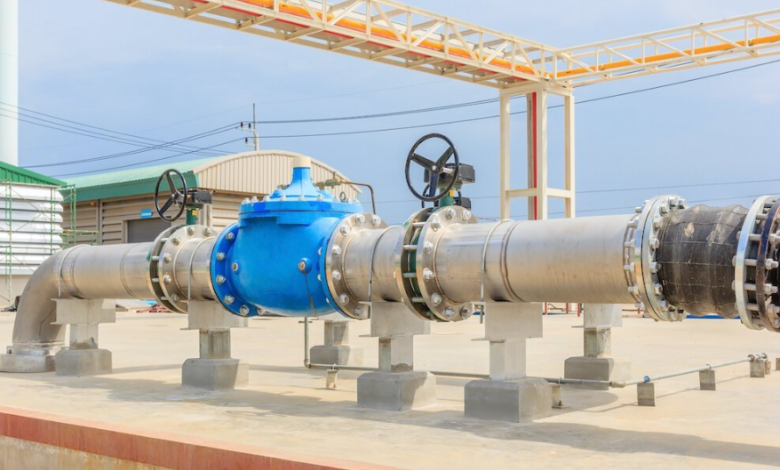
In today’s highly competitive manufacturing and processing environments, companies constantly seek ways to improve operational efficiency, reduce waste, and maintain high product quality. One of the most innovative technologies supporting these goals is the double pig system. Specifically, understanding the double pig system working principle reveals why it is increasingly adopted in industries like food processing, cosmetics, pharmaceuticals, chemicals, and paints.
Unlike conventional single-pig systems, the double pig system incorporates two pigs that work together to maximize product recovery, enhance cleanliness, and ensure a seamless transition between different products in the same pipeline. This article explores the double pig system working principle, its components, applications, advantages, and why it’s a game changer for industries using piggable transfer systems.
What Is a Double Pig System?
A double pig system is an advanced form of pigging technology where two pipeline pigs are used in sequence during the product transfer and cleaning process. The pigs are typically flexible, cylindrical devices made of food-grade or industrial-grade elastomers that travel through pipelines to push product, separate materials, or clean the inner surfaces.
The double pig configuration is specially designed to enclose a volume of product—or “product slug”—between two pigs. This technique allows for greater control over the product flow, minimizes waste, prevents contamination, and supports cleaner product changes without manual line cleaning.
See also: IT Support Services to Keep Your Technology Running Smoothly
Understanding the Double Pig System Working Principle
At the core of the double pig system working principle is the concept of isolating a product slug between two pigs, allowing it to be transported cleanly and efficiently through a pipeline. Below is a step-by-step breakdown of how it operates:
1. Pig Loading into the Pipeline
Two pigs are inserted into the pipeline using a pig launcher. The first pig (leading pig) enters the pipeline and is followed by a slug of product. The second pig (trailing pig) is then launched to close the product slug between them.
2. Formation of the Product Slug
The fluid or semi-viscous product to be transferred is sandwiched between the two pigs. This creates a contained slug that does not mix with the pushing medium (typically air or nitrogen) or the previous/next product in the line.
3. Pushing Medium Propulsion
A pushing medium—usually compressed air, inert gas, or water—is applied behind the second pig. This drives both pigs and the enclosed product slug forward through the pipeline toward the receiving end.
4. Controlled Product Delivery
The pigs travel through the line at controlled speeds, maintaining pressure and minimizing friction. The product between the pigs is delivered precisely to the destination tank or filling system.
5. Receiving and Pig Recovery
Once the pigs reach the pig receiver at the end of the pipeline, the product is delivered, and both pigs are removed. If the system is automated, sensors detect the pigs’ arrival, triggering the stop of the pushing medium.
This is the essence of the double pig system working principle—a precisely engineered sequence that isolates, moves, and recovers product efficiently.
Components of the Double Pig System
To implement this system, several specialized components work together to ensure efficiency and safety:
- Pig Launcher: Device for inserting pigs into the pipeline.
- Pig Receiver: Unit for catching and removing pigs after the process.
- Pigs: Made from sanitary or industrial elastomer materials, these devices must be flexible and durable.
- Pushing Medium Supply: Typically compressed air or nitrogen used to propel the pigs and product.
- Valves and Sensors: Full-bore valves allow pigs to pass through. Sensors track pig location and system pressure.
- Control System: PLC or SCADA-based controls to automate pig launching, pig tracking, and pressure monitoring.
Applications of the Double Pig System
The double pig system working principle is applicable across a wide range of industries:
🧴 Cosmetics and Personal Care
In manufacturing lotions, creams, and gels, cleanliness is critical. The double pig system prevents cross-contamination between product batches and reduces cleaning requirements.
🧃 Food and Beverage
Producers of viscous products like sauces, syrups, and dairy beverages use this system to maximize product recovery and adhere to stringent hygiene standards.
🧪 Pharmaceuticals
In pharmaceutical liquid processing, the system helps avoid mixing drugs or formulations, preserving dosage integrity and purity.
🎨 Paints and Coatings
Chemical manufacturers, particularly those producing multiple paint colors or chemical formulas, use the double pig system to avoid residue build-up and contamination.
Advantages of the Double Pig System
Understanding the double pig system working principle sheds light on its many benefits:
✅ High Product Recovery
Up to 99.5% of product can be recovered from the pipeline, especially useful for high-cost or specialty materials.
✅ Cleaner Product Changeovers
The system virtually eliminates the need for extensive cleaning between product batches, saving time and cleaning agents.
✅ Reduced Water and Chemical Use
Because of minimal product residue, the need for clean-in-place (CIP) systems is drastically reduced.
✅ Superior Hygiene
Since product doesn’t come into contact with air, oxygen-sensitive or microbial-prone products are handled safely.
✅ Environmental Compliance
Lower waste and chemical usage make the system more environmentally friendly and compliant with regulatory requirements.
Future Outlook of Double Pig Systems
The double pig system working principle continues to evolve, driven by advancements in automation, smart sensors, and material science. Some future developments include:
- Smart Pigs: Embedded RFID or tracking chips to provide real-time location and diagnostics.
- Predictive Maintenance: AI-powered systems that use data from sensors to predict maintenance needs before issues arise.
- Eco-Friendly Pig Materials: Biodegradable or recyclable pigs to align with sustainability goals.
These innovations ensure that double pig systems will remain a cornerstone of modern pipeline processing for years to come.
Conclusion
The double pig system working principle offers an elegant and highly effective solution to challenges faced in fluid processing and product transfer. From hygiene and waste reduction to efficiency and automation, this system excels in every area. For industries where cleanliness, speed, and product recovery are critical, the double pig system represents an investment not just in equipment, but in long-term profitability and sustainability.