Sheet Metal Parts Fabrication: Backbone of Modern Manufacturing
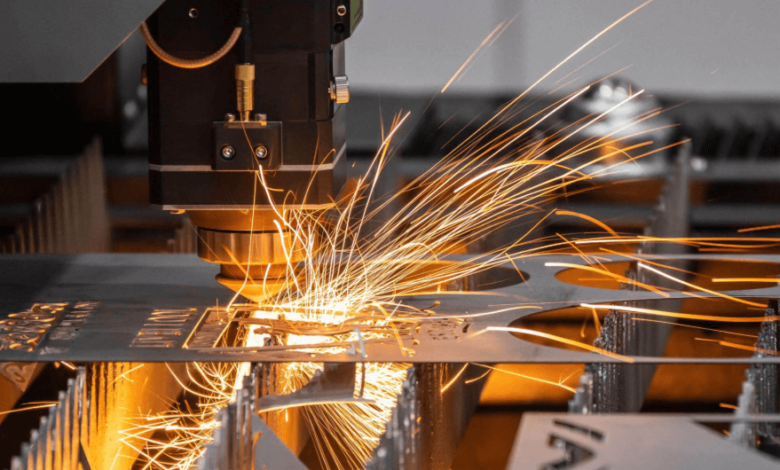
In today’s fast-paced industrial environment, sheet metal parts fabrication plays an indispensable role in shaping the components that drive innovation across industries. From medical devices and consumer electronics to aerospace structures and architectural frameworks, the process of transforming flat sheets of metal into functional, precise components is more critical than ever.
As manufacturers strive for efficiency, quality, and design flexibility, sheet metal parts fabrication stands out as a dynamic solution that bridges creativity with mechanical precision. This article explores the techniques, benefits, applications, and evolving technologies shaping the future of this essential manufacturing service.
What is Sheet Metal Parts Fabrication?
At its core, sheet metal parts fabrication is a collection of industrial processes used to cut, shape, and assemble flat metal sheets into a desired product or component. These sheets are typically made of steel, aluminum, copper, or alloys, and their thickness can vary depending on application.
The fabrication process generally involves multiple stages, including:
- Cutting (laser cutting, waterjet cutting, or plasma cutting)
- Forming (bending, rolling, punching)
- Welding and joining
- Finishing (powder coating, anodizing, polishing)
Whether producing electrical enclosures, chassis, panels, or HVAC parts, this fabrication method delivers speed, repeatability, and versatility.
See also: IT Support Services to Keep Your Technology Running Smoothly
Key Processes in Sheet Metal Parts Fabrication
1. Laser Cutting
Laser cutting uses high-powered lasers to make precise, clean cuts in metal sheets. This method is ideal for detailed designs and tight tolerances. It’s non-contact, meaning the material doesn’t experience much distortion.
2. CNC Bending and Forming
Bending machines and press brakes shape the metal into angles or curves. CNC (Computer Numerical Control) ensures consistent and repeatable accuracy across large batches.
3. Punching
Punch presses create holes or slots in the metal using a die. This process is fast and economical, especially for repetitive patterns.
4. Welding
Joining individual pieces is crucial to creating complex assemblies. MIG, TIG, spot, and robotic welding are all commonly used in sheet metal parts fabrication.
5. Finishing
A part’s surface finish is not just cosmetic—it protects against corrosion and wear. Depending on the end-use, processes like powder coating, painting, plating, or brushing may be applied.
Materials Used in Sheet Metal Fabrication
The choice of metal depends on strength, flexibility, conductivity, corrosion resistance, and cost. Common materials include:
- Aluminum – Lightweight, corrosion-resistant, and easy to work with.
- Stainless Steel – Strong and corrosion-resistant, ideal for food-grade or medical applications.
- Mild Steel – Cost-effective and suitable for general-purpose use.
- Copper and Brass – Conductive and often used in electrical and decorative applications.
Advantages of Sheet Metal Parts Fabrication
✅ Design Flexibility
Modern sheet metal parts fabrication allows for the production of simple to complex geometries, with the ability to quickly iterate on prototypes.
✅ Durability
Fabricated metal components offer strength and resilience, making them ideal for demanding environments like aerospace, automotive, or industrial machinery.
✅ Scalability
Fabrication processes can easily scale from low-volume prototypes to mass production without major changes in workflow.
✅ Cost-Efficiency
Once tooling and programming are set up, automated processes ensure consistent output with minimal labor, reducing per-unit cost.
✅ Customization
Custom sheet metal components can be fabricated to meet exact specifications, including dimensions, cutouts, mounting holes, and surface finish.
Applications Across Industries
The versatility of sheet metal parts fabrication lends itself to nearly every industry:
- Automotive: Panels, engine covers, brackets, dashboards
- Aerospace: Lightweight interior components, mounts, structural reinforcements
- Electronics: Enclosures, housings, cable trays
- Construction: Ventilation ducts, roofing elements, wall panels
- Medical: Sterile equipment trays, surgical carts, workstations
- Telecommunications: Signal cabinets, server racks, heat sinks
As industry demands for miniaturization and structural integrity grow, the importance of precision-fabricated parts becomes even more pronounced.
Role of Technology in Modern Fabrication
Today’s sheet metal parts fabrication industry is driven by digital technology and automation. Here are some innovations revolutionizing the sector:
1. CAD/CAM Integration
Designs created in Computer-Aided Design (CAD) software are directly fed into Computer-Aided Manufacturing (CAM) systems. This seamless integration improves production accuracy and reduces manual errors.
2. Industry 4.0 and Smart Factories
Connected machinery and sensors provide real-time data on performance, tool wear, and production status. Predictive maintenance and data analytics help improve efficiency and reduce downtime.
3. Automated Material Handling
Robotic arms and conveyors speed up loading, unloading, and sorting tasks, reducing human intervention and the risk of errors.
4. 3D Printing Hybrid Solutions
Some advanced facilities use additive manufacturing alongside traditional fabrication to produce jigs, fixtures, or complex part geometries not feasible with standard processes.
Choosing the Right Fabrication Partner
If your business depends on reliable, high-quality metal parts, choosing a trusted sheet metal parts fabrication provider is essential. Here are key factors to consider:
✅ Capabilities
Check for a full-service shop offering cutting, bending, welding, and finishing. Multi-process capability reduces lead time and ensures quality control.
✅ Experience
Look for partners with a track record in your industry. Prior knowledge can help optimize your designs for manufacturability.
✅ Certifications
Ensure the company follows industry standards like ISO 9001 for quality assurance and, where applicable, ISO 13485 for medical-grade components.
✅ Turnaround Time
Timely delivery is crucial in lean manufacturing. Ask about lead times, batch processing capabilities, and shipping arrangements.
✅ Customer Support
Responsive support during quoting, design feedback, and post-sales service can make a big difference—especially in complex or custom projects.
Sustainability and Sheet Metal Fabrication
Sustainability is more than a buzzword—it’s a manufacturing imperative. Fortunately, sheet metal parts fabrication supports eco-friendly practices in multiple ways:
- Efficient use of material: Nesting software maximizes usage and reduces scrap.
- Recyclable metals: Steel and aluminum are 100% recyclable.
- Eco-friendly finishes: Low-VOC coatings and water-based paints are now common.
- Energy-efficient machinery: New laser cutters and CNC presses are designed for minimal power consumption.
Final Thoughts
From prototyping a new product to mass-producing structural components, sheet metal parts fabrication delivers unmatched flexibility, strength, and precision. As the industry continues to adopt smarter tools and greener practices, the potential for innovation only grows.
Whether you’re designing aerospace brackets, medical equipment casings, or sleek consumer electronics, turning to a qualified sheet metal fabrication partner ensures your vision becomes a reality—on time and on spec.